Short delivery terms by using ultra high-speed air turbine spindle with 50000 rpm.
We propose the best and the fastest plan.
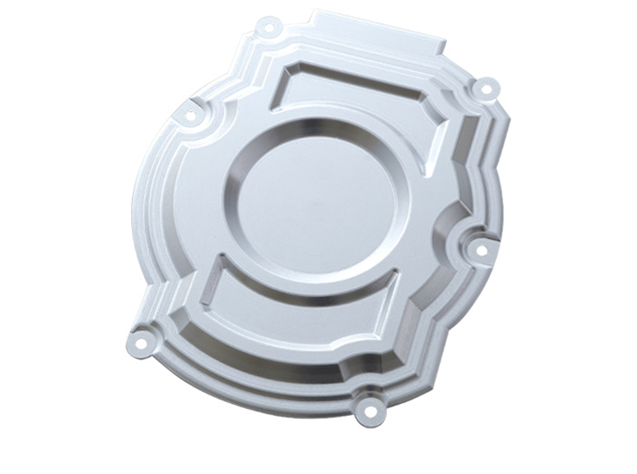
Purpose | Prototype production of housing for Electric VVT Drive Unit |
Processing Method | ADC12 machining |
Size | Diameter 120mm Thickness 20mm |
Delivery terms | One month |
Quantity | 60 |
We were contacted by a person in the Quality Assurance Department, who is in charge of the jig production for testing, about the prototype production of 60 housings for the electric VVT unit. It was the biggest order ever for us.
Customer’s requests and solutions
It was a request received from a major local automotive parts company.
We were contacted by a person in the Quality Assurance Department, who is in charge of the jig production for testing, about the prototype production of 60 housings for the electric VVT unit. It was the biggest order ever for us.
We usually manufacture and deliver 10 to 20 units of ADC12 machining products approximately within 2 weeks, so we were concerned that we may not be able to receive orders for our other customers, once we accept this order which is 3 times or more than our usual production volume in a month.
In addition, we normally use plaster casting for such large orders. However, the customer requested us to manufacture them by ADC12 machining in order to do testing using the prototypes in a short time before mass production, even if it costs more than manufacturing by plaster casting. We suggested the best and the fastest plan.
Proposal 01 / 24 hours operation of the limited production line
We scheduled to operate one production line 24 hours a day, while keeping the other lines for our other customers. The main facility we used was the ultra-high-speed air turbine spindle with 50000 rpm, which we newly introduced. We proposed this production plan which we believed shortens the machining time.
Proposal 02 / We suggest the best “possible” plan.
Using the highly efficient facility was not good enough to meet the delivery deadline because we were required to make 6 deliveries in total, so we needed to deliver 10 prototype units each time to meet the customer’s testing date. We could not produce all 60 units in one go, so we needed to change over the production line every time we complete the production of 10 units.
We scheduled the change-over in the daytime, so we were able to operate the machine without any attendance of our engineers at night. With this schedule we managed to meet the deadlines for 6 deliveries.
Point / Air Turbine Spindle with 50000rpm
The design specification requires machining with a sharp spindle, like a sharpened pencil. The spindle is likely to break due to cutting resistance, unless the rotation speed is high enough, considering the sharpness of the spindle. Sharper spindles require higher rotation speed. Using the air turbine spindle rotating at 50000rpm with compressed air, we completed the prototype production very efficiently without any tool breakage.
Achievement / Customer’s feedback
We delivered the prototypes as per the requested delivery schedule. The customer thanked us for completing the delivery on time, even with the development being behind the original schedule.